Sewing the masterpiece you have in mind perfectly to the last detail will bring you pride and joy that words can not describe. It’s a feeling reserved to those who really enjoy and appreciate the art of sewing. Vacuums R Us & Sewing too in Boulder can help you prevent a broken or worn-out sewing machine by offering regular service and maintenance.
Vacuums R Us & Sewing Too – Boulder Store
3005 28th St
Boulder, CO 80301
Corner of 28th & Valmont in front of Rayback Collective
(303) 449-8913
Handing your machine over to a trained professional will be your best bet to get all your problems effectively and swiftly sorted. We at Vacuums R Us & Sewing Too–Boulder Store have serviced and repaired countless sewing units for over 18 years. If you are indeed looking for sewing machine repair in Boulder, our team of certified specialists are more than happy to offer you their services.
- Certified Woman Owned Small Business
- Local Colorado company
- Average turn around within 14 days.
- Factory authorized Viking Husqvarna service
Our sewing machine service center at Boulder also offers a rigid 90-Day warranty for all services carried out. But truth be told, our customers rarely use it because we strive to get every issue fixed right on the first go.
$89.99 Mechanical Sewing machine tune up!
* Parts extra. Restrictions apply. $119.99 for computerized machines.
Choose a method to receive this coupon and more!
By clicking “Sign up” you agree to allow us to send this coupon via the email or phone number you provide followed by a maximum of three text messages/month and/or 15 emails/year with related coupons, offers, and sales. Unsubscribe at any time by texting STOP or clicking unsubscribe. Message and data rates may apply. We do not share our customer’s information with any other companies.
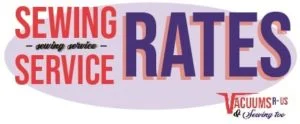
SEWING MACHINE SERVICE INCLUDES:
TENSION ADJUSTMENT, NEEDLE BALANCE, CLEANING, OIL, GREASE
SEWING MACHINE TYPE & SERVICE PRICE
MECHANICAL MACHINES $99.99
COMPUTERIZED MACHINES $149.99
SINGLE NEEDLE EMBROIDERY MACHINES $179.99
MULTI-NEEDLE EMBROIDERY MACHINES $279.99
LONG ARM MACHINES $249.99
SERGER/OVERLOCK MACHINES $149.99
FRONT OF HOUSE DIAGNOSTIC FREE
BENCH DIAGNOSTIC $45

Although we are an authorized service center for Singer, Janome, Viking Husqvarna, Elna, and Elnitta we also maintain other brands such as Juki, Baby Lock, Necchi, Brother, and Kenmore. We could go on, but then this article would just be a list of brands we repair. However, if you are curious about all our services, you can see more info here.
Despite all the sewing machines we take care of, this article will focus on our Viking Husqvarna sewing machine repair and maintenance process.
Regular Sewing Machine Maintenance- Is It Necessary?
Usually, most people have their sewing machines looked at by a trained professional only when it requires a repair. While it does take care of any prevailing problems, it’s not recommended that you do this.
A sewing machine needs to be serviced by trained specialists every 12 to 18 months for it to function at its best. Further, a sewing machine that does not run at its optimum condition will lead to problems and finally cause you to replace the entire unit.
Sewing machines comprise many moving parts that work in unison to provide the perfect stitch you are looking for. Therefore, any fault in any of these mechanisms will bring about a bad sewing experience.
Most of these moving parts require oil or some sort of lubricant to function properly. But in time the lubricants dry off, causing friction between active parts. This will lead to damages that can cause many expenses such as a section replacement. However, routine maintenance will prevent you from running into such troubles and also cause your machine to last much longer.
Besides lubricant, dust and dirt also play an active part in causing issues in your sewing machine. They impede the moving parts of your machine which will cause the motor to work harder to get them in motion and also make it consume more power.
Dust will also trap heat within your machine. It will prevent it from cooling off, hence you risk causing internal damage to the system if the machine operates for long periods under this condition.
So, even if regular maintenance seems like a bother, it will be well worth it in the long run.
The “Vacuums R Us & Sewing Too” sewing machine repair procedure
The sewing machine repair process our specialists at the Vacuums R Us & Sewing Too–Boulder Store follow is effective and methodical so that none of your Viking Husqvarna sewing machine issues are overlooked. If by any chance we find your machine non-repairable because of discontinued parts or other similar reasons that are out of our control, there will be no charge. Now then, without further ado, let’s jump right into our in-house sewing machine repair process in Boulder.

Pre-service Trial
Our certified technicians prefer to compare the state of your sewing machine before and after maintenance. Therefore, as soon as they get their hands on your Viking Husqvarna sewing unit, they check the machine for any startup or power troubles and then run a series of stitches.
This allows them to get a good assessment of the current state of your sewing machine. They note down any visible issues and keep them for later comparisons.
Outer Survey
Once they are done with the Pre-service trial, they inspect the external body of your sewing machine. Parts such as the needle plate, hook, bobbin, spool pin, and head wheel are examined for any damages.
Our techs also check for burrs because burrs can cause damage to the thread and also influence the thread tension in the system.
Stress Inspection
Next up is a stress test on both the top and bottom threads. Thread needs to be distributed perfectly with the right amount of tension for the machine to perform as expected.
Any faults in the stress discs or the overall spring tension retention on the machine will cause overlapping stitches and other issues. So we evaluate the stress by moving along the top thread and also making sure that it passes through every mechanism it needs to.
Once we are done inspecting the top thread, we move onto the bottom thread and the bobbin winder. Here we check the bobbin tension along with its speed.
A bobbin needs to feed the bottom thread fast enough to create evenly spaced stitches and have the right amount of tension to avoid loose stitches. If we find any issues here, we make the adjustments and modifications to get it back on track.
Feed Dog Check
The Feed dog plays an important role in getting your stitches right. It feeds the product into the sewing machine on time so that the stitches created are evenly spaced.
Any issue with your feed dog will cause uneven or, even worse, overlapping stitches. None of us are too keen on wasting time removing stitches and ruining the fabric.
So, we test every feature of your feeding mechanism. Generally, a feed dog comprises two feed teeth.
The feed teeth of a Viking Husqvarna sewing machine usually move forward and in reverse and some models even let you elevate and lower them for free handwork. When examining the feed teeth we will check if the feed teeth move in every direction possible and also that the special movement works fine.
Issues With Extra Features
Our techs pay attention to any additional features your sewing machine may offer. Many recent sewing machines come with an inbuilt needle threader. It’s quite useful for anyone having trouble getting the thread into the eye of a needle.
Our specialist will examine the mechanism and do the adjustments needed for proper functioning. If the needle threader cable is damaged beyond repair, they might suggest a replacement. Another handy feature in modern sewing machines is the Automatic Button Holer. Our techs will inspect its functioning as well.
Along with the inspection of extra features, our techs test out your firmware if you’ve got an electronic sewing unit. And if it requires an update, they’ll have it installed by the time the machine is handed back to you.
A Look Inside
Once the outside of your Viking Husqvarna sewing machine is taken care of, we take a look inside. We remove the covers and give the internal chassis a thorough cleaning. The dust and dirt are taken care of while old oil or lubricant is replaced. We make sure that every crevice, even the ones that are hard to reach, is dust/dirt-free.
The oil change of the machine is done with extreme care because we don’t want oil seeping into areas that do not need it. This will do more harm than good.
Once the internal cleaning session is over, we examine the stitching operation and the timing of your machine. A sewing machine uses both the top and bottom thread to form a stitch. It does this by grabbing hold of the top thread when the “top thread” fastened needle punctures the product.
A hook called the shuttle hook grabs hold of the top thread and creates the stitch after a 360 rotation. The needle puncturing the fabric, the shuttle hook grabbing the top thread, and the hook resetting should all be done at the perfect time to create a stitch.
A delay in any of these actions will cause an issue with the stitches. So, we make all the adjustments to get the timing right, including. We also deal with any feed timing issue here.
Post-service Trial
After all the internal problems are taken care of, our techs put the covers back on and give it a nice wipe. They use 100% natural cleaner so that it doesn’t harm the exterior. Our certified specialists then conduct a few tests to assess the current state of the machine.
First, they test out various stitch types like straight stitches, Zig-Zag stitches, and Reverse stitches. They then run the machine at its highest sewing speed to assess the internal workings.
Finally, our technicians go through every additional feature your sewing machine offers to make sure that they are working fine.
There’s way more technical stuff happening on the benches of our professionals, and this is just a peek at it. Nevertheless, we are pretty proud of our sewing machine repair process and got plenty of reviews to back up its success. So, if you are having sewing machine troubles, join us and we’ll solve them all for you!